eROSITA Picture Gallery

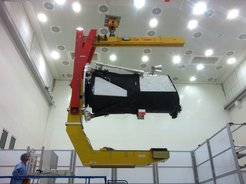
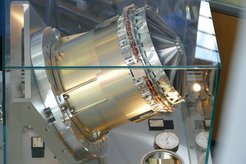
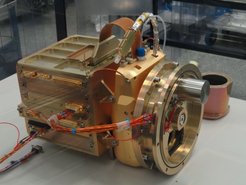
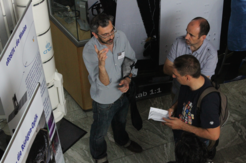
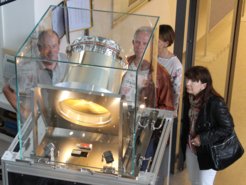
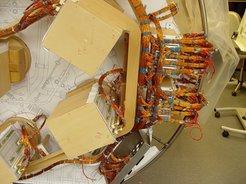
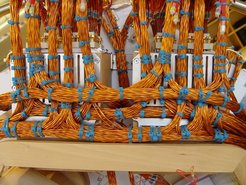
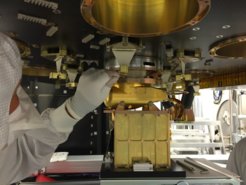

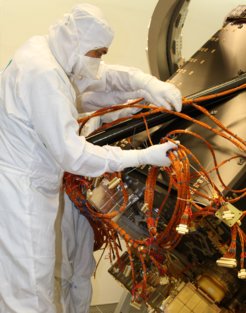
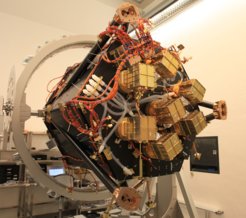
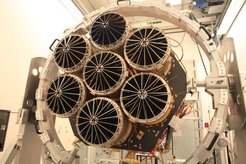
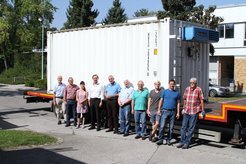
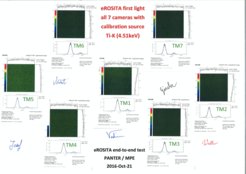

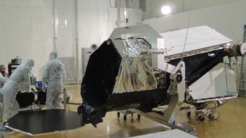
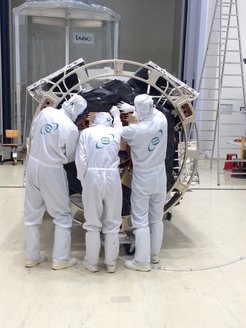


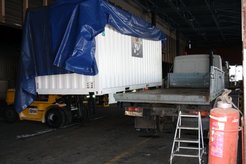
Figure 14: Finally, in January 2017 the fully integrated eROSITA telescope was shipped via cargo plane to Moscow. There it was cold, the roads covered in snow, and the truck a little bit older than we expected!
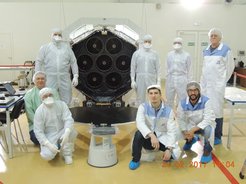
Figure 15: eROSITA made it safely to the integration hall of NPOL Lavochkin, its new home for the following 2 years (credit NPOL).
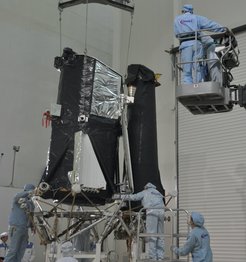
Figure 16: The SRG satellite begins to take shape. In this photo of 2018, for the first time eROSITA and its sister telescope ART-XC (developed by IKI, the Space Science Institute of the Russian Academy of Science) are mounted together on the support.(Credit NPOL)
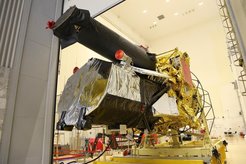
Figure 17: The completed #SpektrRG is ready to go. First to the steppe of Baikonur. (Credit Roscosmos).
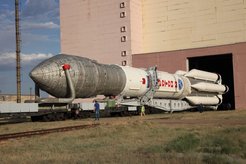
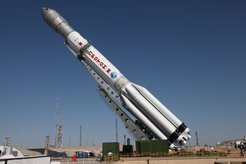
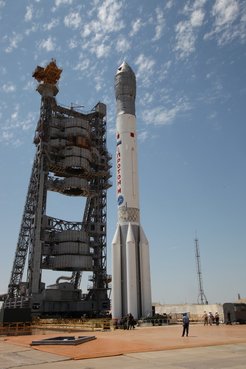

Figure 20: The eROSITA PI, Peter Predehl, in front of the Proton Rocket carrying SRG. Credit: K. Nandra.
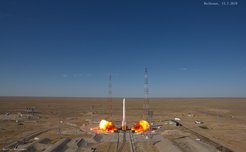
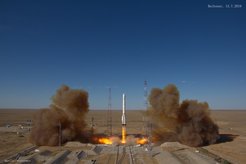
Figure 21 b: July 13, 2019, 12:31 UTC. Credit: Roscosmos.
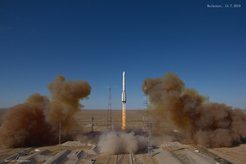
Figure 21 c: July 13, 2019, 12:31 UTC. Credit: Roscosmos.
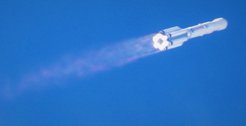
Figure 22: Credit: V. Burwitz
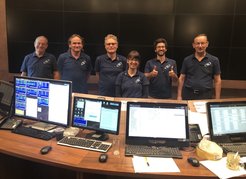
Figure 23: The eROSITA team in the Mission Operation Center at NPOL in Khimki, near Moscow, at the end of the successful launch operations. From left to right: W. Kink, W. Bornemann, S. Müller, M. Fürmetz, D. Coutinho, J. Eder.
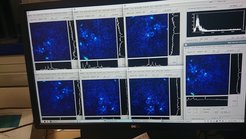
Figure 24: The eROSITA First Light image (LMC) forms on the MPE control room screens.

Figure 25: Celebrating eROSITA First Light in the MPE eROSITA Control Room. From left to right: M. Salvato, D. Coutinho, A. Predehl, M. Freyberg, W. Kink, N. Meidinger, P. Predehl, G. Hartner, K. Dennerl, E. Pfefferman, A. Merloni, M. Ramos-Ceja, C. Maitra.